Powder coating market and applications
With the continuous advancement of screening technology, high-quality powder coatings are now more achievable, enhancing both performance and application range. Reports indicate that the global powder coating market is expected to grow at an annual rate of 6-7%. The Asia-Pacific region, in particular, stands out as the largest and most promising market for powder coatings.
Powder coatings find wide applications across various industries, including automobiles, home appliances, furniture, and construction materials. The rapid growth of the automotive industry has significantly contributed to the expanding powder coatings market. Known for their excellent wear and corrosion resistance, powder coatings are often used as primers for automotive finishes to enhance the aesthetics of car bodies. Additionally, they provide both protective and decorative functions, making them ideal for indoor and outdoor decoration, metal surface spraying, and more.
Why is the production process of coating powder important?
The production process of coating powder is vital for the long-term success of an enterprise. High-quality products are the cornerstone of a company, enhancing customer loyalty, corporate image, and brand awareness. A well-optimized production process not only improves product quality and performance but also boosts production efficiency, reduces costs, and increases overall profitability. As a critical component of the coating powder production process, the vibrating sieve plays a key role in controlling product quality and particle size distribution, ensuring the consistent quality of the coating powder.
How to choose a powder coating sieving machine
The powder coating sieving machine uses the screen to sieve and separate the coating powder, remove oversized or undersized particles, impurities and contaminants, and obtain coating powder of uniform particle size.
We offer three different types of coating powder sieving machines: one is an Industrial Vibrating Sieving Machine, which can be equipped with an Ultrasonic Deblinding System, the other is a Compact Sieve (compact design, space saving, meets specific spatial requirements), and the last one is a Rotary Sieves.
Industrial Vibrating Sieving Machine
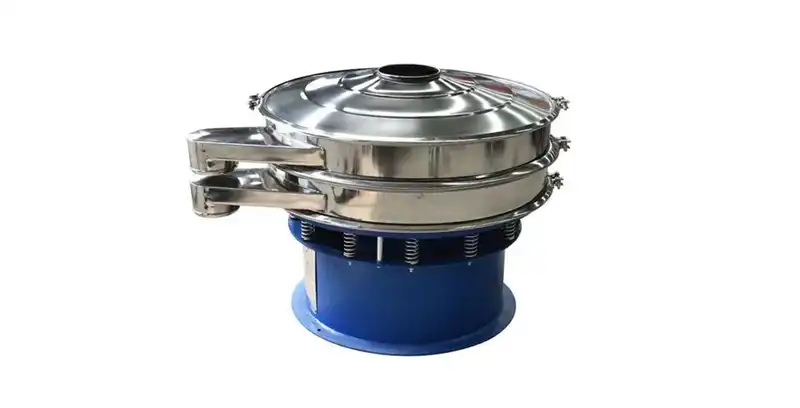
This machine utilizes a vibration motor to convert the motor’s rotational motion into horizontal, vertical, and inclined three-dimensional motion, achieving an effective screening process. Available in various sizes and configurations, the industrial vibrating sifter can be customized with an ultrasonic deblinding system. The combination of the ultrasonic deblinding system and vibration motor enables the screening of fine particles, prevents screen mesh blockage and blinding, and increases screening output. Additionally, a magnetic separator can be added at the feeding inlet or discharge outlet port to prevent foreign iron filings from contaminating the product. Custom solutions can be designed to meet specific customer requirements, ensuring optimal performance and satisfaction.
Compact Sieve
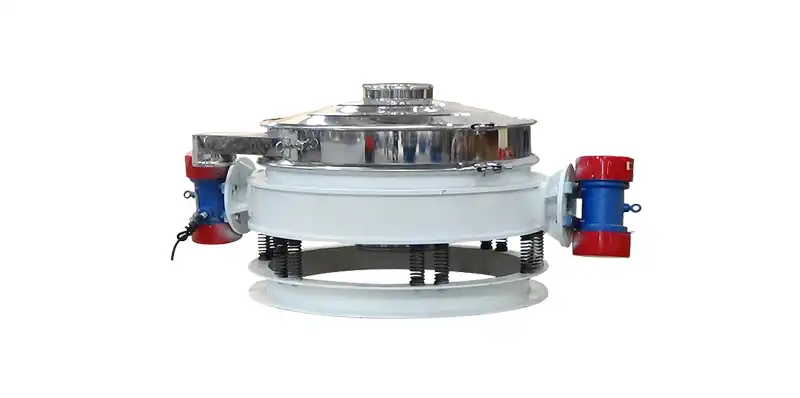
The compact sieve uses a motor as a vibration source to create an elliptical motion on the sieve surface. It comes in two configurations: single motor and dual motor. Its compact design requires minimal space, making it easy to integrate into production lines. The fully sealed structure reduces dust pollution and enhances the working environment.
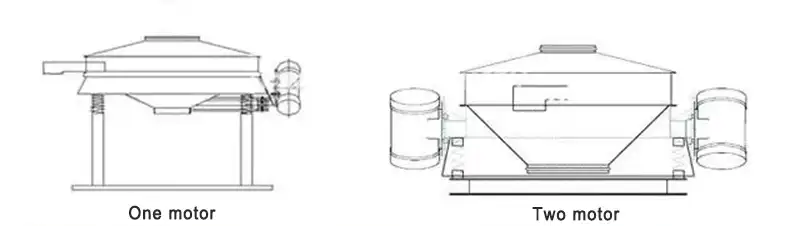
Rotary Sieves
Rotary sieves are ideal for materials with low specific gravity and fine powder. When the material enters the sieving machine, external airflow reduces the agglomeration of the coating powder. The material is then sieved and separated, ensuring it proceeds safely to the next process step with a consistent particle size.
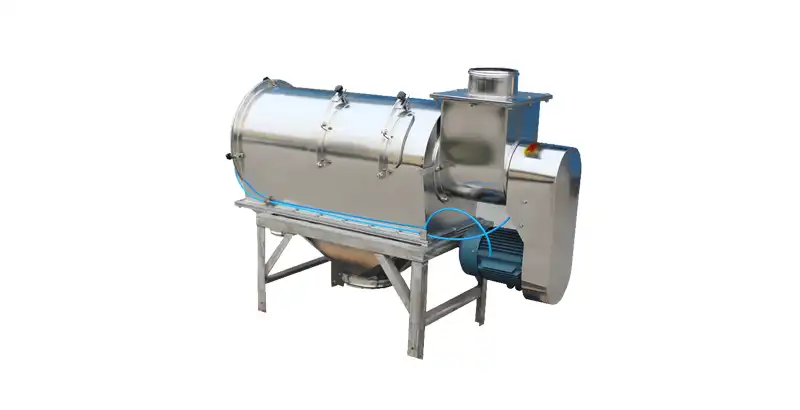
Different screening machines can be customized to accommodate various mesh sizes and space requirements. This customization improves screening efficiency, enhances product quality, reduces production and maintenance costs, and boosts product market competitiveness.
Advantages of Sifter Machines in Powder Coatings
- Consistent Quality: Ensure the consistent quality of coating powder, resulting in high-quality finished products.
- Spraying Efficiency: Prevent clogging of spraying equipment, extend its service life, and achieve uniform coloring on the spraying surface.
- Easy Maintenance: Features an easy-to-clean screen and a quick-open design for convenient screen changes.
- Cost Efficiency: Reduce waste generation, lower costs, and improve process efficiency.
- Impurity Removal: Eliminate agglomerates, lumps, and other impurities while avoiding mesh clogging.
- Versatile Sizing: Available in a full range of screen sizes, from 400mm to 2600mm, to meet various throughput targets.
Customer Benefits
Screening powder coatings minimizes waste generation, ensuring customers receive high-quality coatings with a smooth, high-gloss finish. This process protects equipment from pollution, extending the service life of spraying equipment and reducing downtime. As a result, production efficiency increases while production costs decrease, ultimately enhancing product competitiveness and delivering tangible benefits and cost savings to customers.